本工程区域位置图
项目以煤为原料生产甲醇并进一步加工生产烯烃,同时副产混合C4、硫磺、粗汽油、氯化钠和硫酸钠,生产规模为:200万吨/年煤制甲醇,35万吨/年聚乙烯、55万吨/年聚丙烯(其中16.6万吨/年丙烯来自现有工程)。
现有工程为《中煤陕西榆林能源化工有限公司醋酸系列深加工及综合利用项目》,主要建设内容包括180万吨/年甲醇装置、30万吨/年聚丙烯(PP)、30万吨/年全密度聚乙烯(FDPE)、1.335万吨/年甲基叔丁基醚(MTBE)、1.874万吨/年丁烯-1(其中1.285用作PE共聚体)、4万吨硫磺。该工程于2014年7月建成投产。
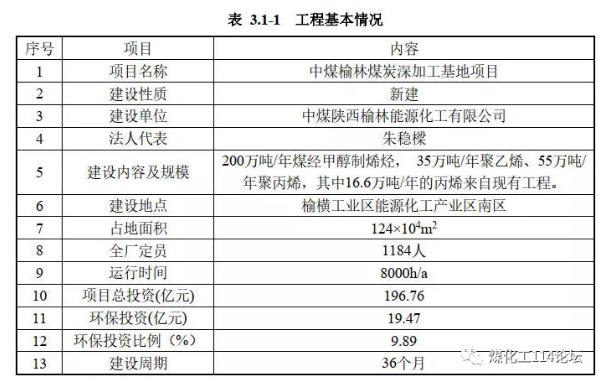
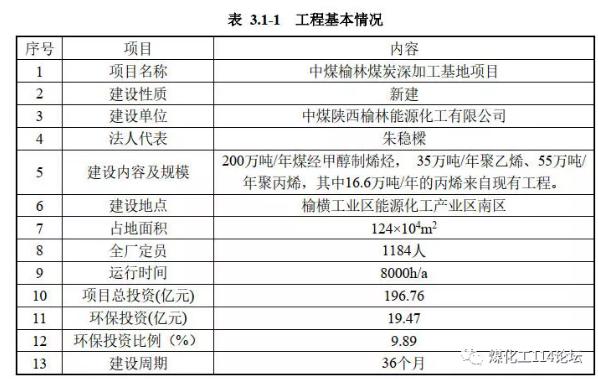
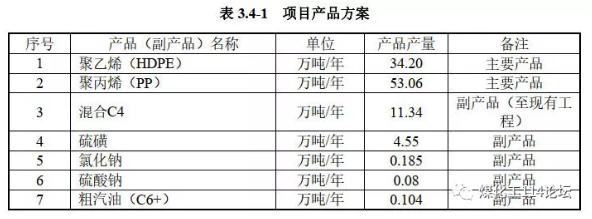
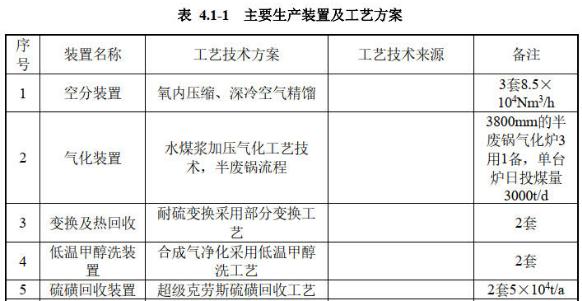
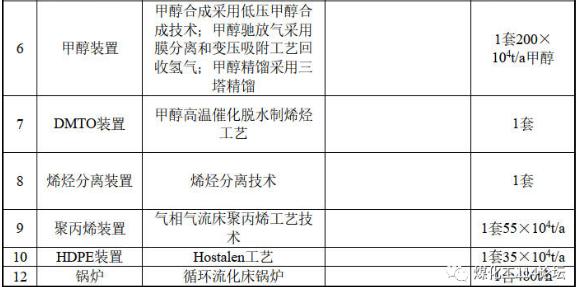
现有工程为《中煤陕西榆林能源化工有限公司醋酸系列深加工及综合利用项目》,主要建设内容包括180万吨/年甲醇装置、30万吨/年聚丙烯(PP)、30万吨/年全密度聚乙烯(FDPE)、1.335万吨/年甲基叔丁基醚(MTBE)、1.874万吨/年丁烯-1(其中1.285用作PE共聚体)、4万吨硫磺。该工程于2014年7月建成投产。
现有工程为《中煤陕西榆林能源化工有限公司醋酸系列深加工及综合利用项目》,主要建设内容包括180万吨/年甲醇装置、30万吨/年聚丙烯(PP)、30万吨/年全密度聚乙烯(FDPE)、1.335万吨/年甲基叔丁基醚(MTBE)、1.874万吨/年丁烯-1(其中1.285用作PE共聚体)、4万吨硫磺。该工程于2014年7月建成投产。
项目由来
为促进陕西省煤炭深加工产业发展,努力探索高效、清沽产业发展之路,陕西省拟由中煤集团投资建设中煤榆林煤炭深加工基地项目。2013年2月22日公司获得了国家发改委《中煤榆林煤炭深加工基地项日于关于开展项目前期工作的复函》(发改办产业(2013)476号),(以下简称“路条”)。
建设单位取得路条后,立刻展开了各项前期研究工作,邀请石化专家、科研机构、设计单位、专利商对技术方案进行了进一步论证,对路方案于说调整,基于8.7兆帕半废锅大型水煤浆加压气化存在极大风险和无工艺包的实际,项目取消8.7兆帕大型水煤浆加压气化示范。基于半废锅流程煤气化副产蒸汽发电技术对比整体煤气化联合循环发电技术(IGCC)在总投资、运行成本、综合能效、可靠性/在线率/维修性、污染物排放上具有一定优势,项日取消整体煤气化联合循环发电技术示范。基于目前二氧化碳駆油尚存在一定环境风险、技术风险和安全风险,二氧化碳捕集示范由驱油变更为生产食品级二氧化碳。基于聚氯乙烯无汞催化剂技术已经成熟,乙烯单体用于电石法聚氯乙烯转型升级己无示范必要性,榆林市无企业利用乙烯单体生产聚氯乙烯实际,产品方案由生产乙烯单体调整为生产聚乙烯。基于顺丁橡胶产能严重过剩和己烯-1生产装置高能耗和操作安全性情况,取消己烯-1和顺丁橡胶产品。同时为落实《能源发展“十三五”规划》要求,推动煤化工行业发展,按照《现代煤化工产业创新发展布局方案对中煤榆林提出的实施煤制烯烃升级改造工程的要求,项目开展了高压水煤浆半废锅气化大型化工程示范,开展煤化工固废源头减量及清洁高质利用新技术研究环保示范任务,同时开展了闭式循环冷却、废水近零排放和水煤浆气化炉协同处置废碱液工程实践。2017年3月中煤陕西公司以中煤陕函(2017)3号文向陕西省发改委提出项目核准的请示(请示附件详细载明了变更内容),2018年4月24日陕西省发改委出具了项目核准文件一一《陕西省发展和改革委员会关于中煤榆林煤炭深加工基地项目核准的批复》(陕发改油气(2018)528号),见附件。
本工程属于《石化产业规划布局方案>贯彻落实工作的通知》发改产业(201547号〕明确的煤制烯烃升级示范项目,属于《现代煤化工产业创新布局方案》确定的优势企业,项目在设计、建设和运行中,按照“环保优先、绿色发展”的目标定位和循环经济、清洁生产的理念,强化各装置节能降耗措施,开展了65MPa半废锅流程水煤浆加压气化大型化工程示范,采用了新型DMTO工艺等能源转换率高、污染排放强度低的工艺技术,总体工艺技术通过对现有工程改造升级,优化项目设计,总体工程二氧化硫、氮氧化物、颗粒物、挥发性有机物分别比现有工程降低了196.55吨、19.2吨、7.91吨、16.59吨,大气污染物实现增产减污。通过采用闭式循环等先进节水技术,闭式循环水量占比由现有工程的0%提升至48.5%,新鲜水耗由现有工程的3.31t煤降低至2.92tt煤,实施了大海则矿井水工程,总体工程矿井水利用比例提升至50.8%,全厂新鲜水使用量由1300万立方米/年降低至1039万立方米/年。现有工程首次突破烯烃废碱液及生化污泥制浆长周期工程化运行技术难点,实现长周期稳定运行,为煤化工行业固体废物“减量化、资源化”,提供了可行技术路径。承担了科技部国家重点研发计划“固废资源化”重点专项项目“煤化工固废源头减量及清沽高质利用新技术研究”示范任务。
1、充分利用现有工程的运行升级改造经验,优化本工程建设,实现本工程高效益、长周期稳定运行
现有工程建设内容和产品方案为:180万吨/年煤制甲醇装置,30万吨/年聚丙烯(PP),30万吨/年聚乙烯(PE)。
现有工程于2014年建成投产,并拥有5年长周期连续稳定运行经验现有工程投产后,追加3亿多元开展了25项废气、废水、固废和节能降耗环保升级改造措施,实现了节能降耗和污染减排。被评为煤化工行业第一家全国智能制造示范企业,在煤制烯烃行业固废资源化、提质增效方面起到引领示范作用。
公司建立了完备的操作管理制度、生产运行管理体系和风险应急预案、环保设施运行管理体系。现有工程的稳定运行高效生产,为各装置生产积累了丰富的实操经验,培养了一批有运行经验的操作人员和技术骨干队伍。
本项目目与现有工程毗邻建设,装置类似,可充分发挥现有工程的技术、人员管理等优势,为本项目稳定生产运行提供基础和保障。同时,现有工程运行中积累了丰富的废水、废气、固废等运行数据,为本项目设计运行的优化提供了可靠的基础资料。
2、开展工程升级示范
本项目低温甲醇洗装置、甲醇合成装置、烯烃分离装置、聚丙烯装置均采用与一期项日相同工艺技术,气化装置拟采用美国GE公司半废锅流程水煤浆加压气化技术,DMTO装置采用中国科学院大连化学物理研究所开发的新型DMIOⅡl技术,高密度聚乙烯装置采用美国利安德·巴塞尔公司淤浆法聚乙烯技术,项目总体工艺技术处于世界先进水平
与有项目相比,本项目工程升级示范主要体现在以下四方面:
1、废锅流程水煤浆加压气化技术,大幅度提高了能量转化效率,并减少污染物排放。气化压力6.5MPa,单炉日投煤量3000吨,副产98MPa、540℃的高压饱和蒸汽625th,气化废锅副产的饱和蒸汽利用燃料气通过加热炉加热后用于发电,既节省了高压蒸汽减温减压损失,也减少了污染物排放(与现有工程相比SO2、NOx和烟尘排放量可降低56%)。
2、现有工程的蒸汽利用进行充分挖潜,减少发电量、优化锅炉建设规模。现有工程设置4×480th循环流化床锅炉+2×100MW汽轮发电机,本项目通过降低现有工程发电负荷匀出蒸汽供新建工程使用,并利用气化废锅过热蒸汽发电在充分考虑项目建设符合园区规划环评要求、园区无配套的集中供热设施的前提下,新建工程仅设置1台480th循环流化床锅炉(比现有工程减少3台480th循环流化床锅炉)·既可与现有工程锅炉互为备用,便于全厂整体蒸汽调整,又有利于化工装置安全平稳生产,减少非正常工况的环境影响。
3、以环境质量改善为核心的环境管理要求,通过现有锅炉超低排放改造、低温甲醇洗尾气处理措施改造、硫回收装置液硫脱气改造、装车站台增设油气回收、污水处理站加盖密闭除臭改造等多项“以新带老”措施,大幅度减少污染物排放。
4、照不同工艺要求,循环水冷却系统采用闭式循环和开式循环水系统相结合的方式;聚乙烯、聚丙烯装置全部采用闭式循环系统:DMTO、锅炉等装置采用直接空冷方式,年均节约用水约486万吨。
5、含盐废水采用最新的蒸发结晶分盐技术,全部废水将实现不外排。
6、结现有工程废碱液、生化污泥至气化炉掺烧的难点和经验,进“优化废碱液和生化污泥协同处置过程中的问题,实现煤化工行业废碱液和生化污泥采用水煤浆气化炉协同处置、闭式消纳、长周期运行的处置流程和关键控制参数的研宄总结,减少煤化工行业大量危险废物需处理处置的压力,并有效降低填埋焚烧处置造成的二次污染,提升煤化工清洁生产水平。
3、承担高压水煤浆半废锅气化大型化工程示范
水煤浆加压气化技术主要是激冷流程气化技术,半废锅流程气化运行业绩较少,截止2014年,国内外已有运行业绩的类似加压水煤浆气化半废锅工艺的最高操作压力为4.5MPa,且仅在美国有示范项目。近年来,国内半废锅流程水煤浆加压气化技术已有较大进步,采用半废锅流程的晋华炉技术开发成功,并应用于河南金大地合成氨项目中,气化压力6.5MPa,投煤量1500吨/天;华东理工大学和兖矿国拓联合开发的半废锅流程多喷嘴对置式水煤浆加压气化技术已应用于兖煤榆林聚甲氧基二甲醚项目中,气化压力6.5MPa,投煤量2000吨/天(尚未投产)。本项日己于2014年完成GE半废锅流程气化技术的采购,单炉投煤量高达3000吨/天,因此本工程65MPa的半废锅流程水煤浆加压气化技术目前仍具有很好的工程示范意义。
此外气化热量通过辐射锅炉副产9.8MPa蒸汽,副产蒸汽利用燃料气通过加热炉加热用于发电,既节省了高压蒸汽减温减压损失,也减少了污染物排放。同现有工程相比,本工程采用半废锅流程气化技术,年产60万吨烯烃可减少燃粒煤102.88th,并副产625th的过热蒸汽,在现有工程和本工程均执行超低排放标准限值的情况下,本工程半废锅副产过热蒸汽仍可减少二氧化硫的排放量190氯氧化物排放量283ta、.烟尘排放量57ta,污染物减排56%。
4、承担煤化工固废源头减量及清洁高质利用新技术研究环保示范
本项目拟承担“煤化工固废源头减量及清洁高质利用新技术研究”示范任务,目前该示范项目已通过科技部国家重点研发计划“固废资源化”重点专项2019年度指南项目安排公示,项目编号“2019yYFC1905100”,中煤陝西公承工污泥结构解聚及束缚水定向转换技术硏究”和“气化细灰高碳组分和化工污泥与煤协同制浆硏究及示范”两个课题任务。
项目以气化细灰和化工污泥与煤协同制浆为主线,以实现分质高值、高效利用为目标,开发化工污泥结构解聚及束缚水定向转换技术、多源煤化工固废与煤协同制浆技术并建成示范线。研究高效精准转化与清洁利用新机制与新方法,形成气化细灰与化工污泥清洁分质高值利用新技术及产品体系,构建煤化工典型难处理固废近零排放的“无废型”绿色新流程。对行业此类危废的气化协同处置的提升起规范指导的引领作用。
5、采用先进的环保措施,执行最严格环保标准
本项目采用先进的生产工艺源头上减少污染物的产生,并采用先进的环保措施和最严格的环保标准,降低污染物的排放。
本项目建设所在地榆林市为大气污染物排放一般控制区,考虑到环保要求的日趋严格及项目建设后需改善区域环境质量的要求,大气排放标准按照特别排放限值执行。同时污水处理场采用封闭+生物处理工艺处理恶臭气体;锅炉烟气执行超低排放标准。生产废水收集处理后全部回用,不外排。废碱液、生化污泥送气化装置磨煤制浆资源化利用,煤化工固废源头减量及清洁高质利用新技术研究示范任务,可减少危险废物外委处置量82204t/a,将对煤化工行业的固废处置及资源化利用起到引领示范作用。
6、生产工艺先进,清洁生产水平高
本项目采用6.5MPa半废锅流程水煤浆加压气化技术,气化过程副产大量饱和蒸汽,新建动力站锅炉规模配置降低了67%,循环水站优先使用闭式循环冷却系统。能源清洁转换效率为46.12%,新鲜水耗2.92tt标煤,满足国家发展改革委“关于做好《石化产业规划布局方案》贯彻落实工作的通知”(发改产业[2015]1047号)能源清洁转换效率高于44%,新鲜水耗低于3t标煤的要求。单位产品能源能耗为2056tct,单位产品新水量为1152tt,达到发改委发布的《现代煤化工产业创新发展布局方案》(发改产业o17153号)中单位烯经严综各能耗低于2.8吨标煤(按《煤制烯烃单位产品能源消耗限额》(GB30180)方法计算)、新鲜水耗小于16吨的要求。