与此同时,煤制乙二醇产能也已经占据中国乙二醇产能的重要比例。亚化咨询《中国煤制乙二醇年度报告2018》数据显示,至2018年一季度,中国已投产石化乙烯路线乙二醇装置19套,总产能495万吨;MTO乙烯路线乙二醇装置2套,总产能78万吨,合成气草酸酯路线乙二醇装置17套,总产能300万吨。
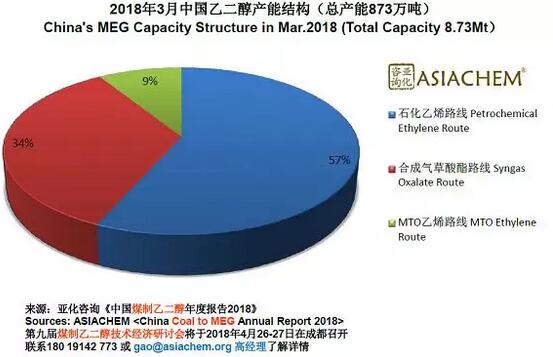
2017年,中国已投产煤制乙二醇项目已经普遍实现了高负荷稳定运行。在此背景下,2017-2018年,草酸酯路线煤制乙二醇的技术研发正在向大型化、低成本、高选择性、长催化剂寿命和环境友好的方向发展。
——大型化
现有已投产运行合成气草酸酯路线煤制乙二醇(CTMEG)装置单台草酸二甲酯(DMO)反应器产能普遍为6-8万吨/年DMO,单台DMO加氢制MEG反应器产能普遍为5万吨/年MEG。较小的列管式羰化反应器及列管式加氢反应器规模,造成CTMEG装置工程投资高、运行能耗高、副产物多、生产负荷低、蒸汽消耗大等缺陷。
目前,领先的煤制乙二醇技术提供商正在积极开展反应器大型化工作,将单台DMO反应器产能提升至10-20万吨/年,单台MEG反应器产能提升至7.5-10万吨/年,预计将于2018年实现工业化。
此外,公开资料显示,南京敦先化工科技有限公司开发成功大型化径向蛇管式羰化反应器及径向球腔联箱蛇管式加氢反应器取代现有列管式羰化及加氢反应器,对于一套20万吨/年乙二醇规模装置,可降低两亿元左右的工程投资,每年因降低反应器阻力及降低精馏装置蒸汽消耗的两项节能,可节省8000万元以上运行费用。另外,还可以延长催化剂的使用寿命,实现乙二醇装置的长周期满负荷运行。
——工艺优化进一步降低成本
在反应器大型化之外,通过工艺优化可以进一步降低CTMEG的成本。
通过稀硝酸还原工艺,可以减少危废硝酸盐生成,并减少含盐废水排放量,工艺废水更易达标排放,从而降低环保成本,保障生产设备长周期安全运行。
优化副产品回收工艺,可以提高收入。通过在DMO合成工段增加DMC回收和分离单元,可以获得工业级DMC副产品;在乙二醇精馏工段可以回收获得乙醇和二元醇副产品。
通过改进工艺流程和优化能量利用,可以降低装置能耗,并减少碳排放。
——高选择性、长寿命和环境友好的催化剂
目前领先的煤制乙二醇技术提供商DMO催化剂可以实现大于99%的选择性,加氢催化剂选择性也大于98%,两种催化剂实际使用寿命都超过预期。在此背景下,领先的煤制乙二醇技术提供商们正在持续改进催化剂,例如进一步改善羰基化催化剂的传质传热,进一步降低加氢催化剂的微量杂质的选择性等。
——大型化
现有已投产运行合成气草酸酯路线煤制乙二醇(CTMEG)装置单台草酸二甲酯(DMO)反应器产能普遍为6-8万吨/年DMO,单台DMO加氢制MEG反应器产能普遍为5万吨/年MEG。较小的列管式羰化反应器及列管式加氢反应器规模,造成CTMEG装置工程投资高、运行能耗高、副产物多、生产负荷低、蒸汽消耗大等缺陷。
目前,领先的煤制乙二醇技术提供商正在积极开展反应器大型化工作,将单台DMO反应器产能提升至10-20万吨/年,单台MEG反应器产能提升至7.5-10万吨/年,预计将于2018年实现工业化。
此外,公开资料显示,南京敦先化工科技有限公司开发成功大型化径向蛇管式羰化反应器及径向球腔联箱蛇管式加氢反应器取代现有列管式羰化及加氢反应器,对于一套20万吨/年乙二醇规模装置,可降低两亿元左右的工程投资,每年因降低反应器阻力及降低精馏装置蒸汽消耗的两项节能,可节省8000万元以上运行费用。另外,还可以延长催化剂的使用寿命,实现乙二醇装置的长周期满负荷运行。
——工艺优化进一步降低成本
在反应器大型化之外,通过工艺优化可以进一步降低CTMEG的成本。
通过稀硝酸还原工艺,可以减少危废硝酸盐生成,并减少含盐废水排放量,工艺废水更易达标排放,从而降低环保成本,保障生产设备长周期安全运行。
优化副产品回收工艺,可以提高收入。通过在DMO合成工段增加DMC回收和分离单元,可以获得工业级DMC副产品;在乙二醇精馏工段可以回收获得乙醇和二元醇副产品。
通过改进工艺流程和优化能量利用,可以降低装置能耗,并减少碳排放。
——高选择性、长寿命和环境友好的催化剂
目前领先的煤制乙二醇技术提供商DMO催化剂可以实现大于99%的选择性,加氢催化剂选择性也大于98%,两种催化剂实际使用寿命都超过预期。在此背景下,领先的煤制乙二醇技术提供商们正在持续改进催化剂,例如进一步改善羰基化催化剂的传质传热,进一步降低加氢催化剂的微量杂质的选择性等。
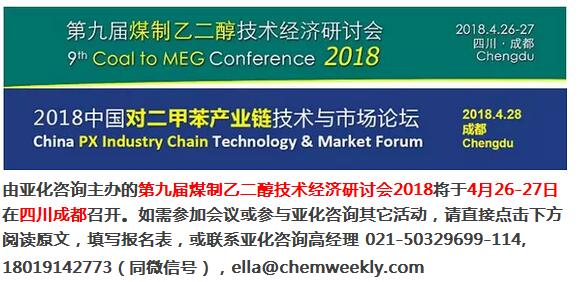